Product Introduction
The unique design of Shanghai Leadbell LB910 automatic cleaning robot provides an efficient and energy-saving waterless cleaning solution for your photovoltaic power station. It can exchange for higher power generation efficiency at lower cost and has very good investment income. It can make your photovoltaic power plant always in the best power generation state.
The LB910 robot is a fully automatic photovoltaic panel cleaning system that does not require any manual intervention and operation on site. It automatically cleans the photovoltaic panels every day or every few days according to a preset program, and it charges itself and runs automatically.
The LB910 robot is suitable for various types of photovoltaic power stations, from distributed power stations of several kilowatts to large-scale ground photovoltaic power stations of hundreds of megawatts. It adopts a modular design, and the length of the robot can be customized according to the on-site array situation to adapt to photovoltaic arrays of different widths. It is easy to maintain and designed for outdoor electric fields.
Cleaning Process
1. Start cleaning from the parking space
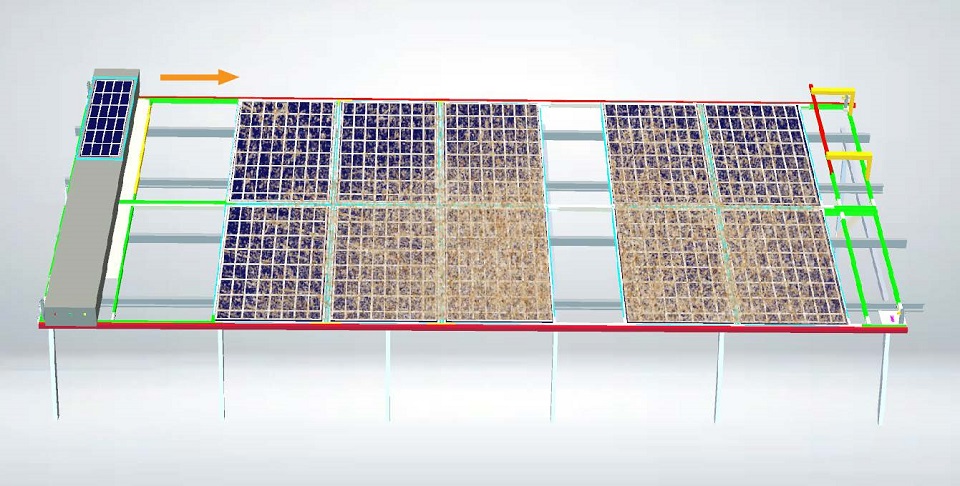
2. Cleaning in progress
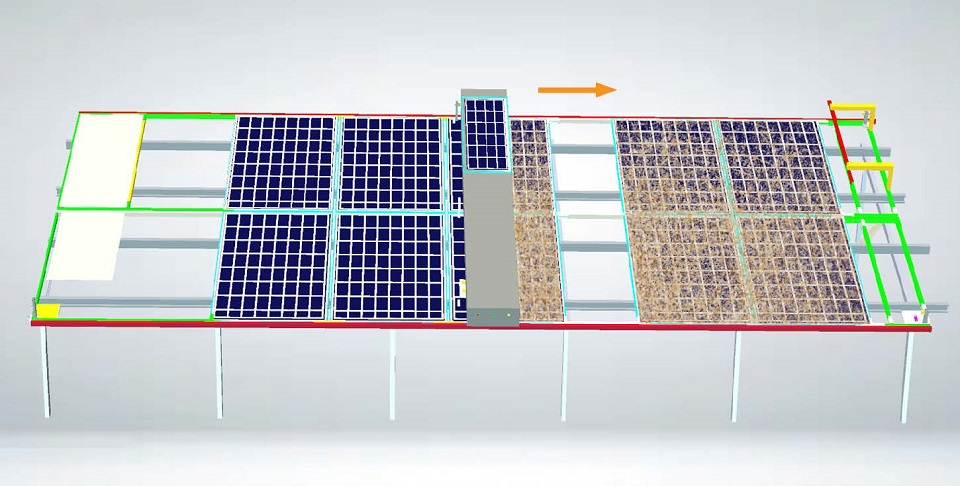
The LB910 robot moves along the upper and lower edges of the photovoltaic array, and the high-speed rotating roller brush can clean the dust on the surface of the module. In order to ensure the stable and smooth operation of the robot, and to protect the photovoltaic modules from crushing, it is necessary to install guide rails on the upper and lower ends of the photovoltaic panel array, and the robot moves along the guide rails. Sometimes, we just install small bridge rails between the components on the upper and lower sides of the photovoltaic panel array to reduce the vibration of the photovoltaic components when the robot is walking, and it can also protect the photovoltaic components.
3. The robot reaches the reversing position, ready to back
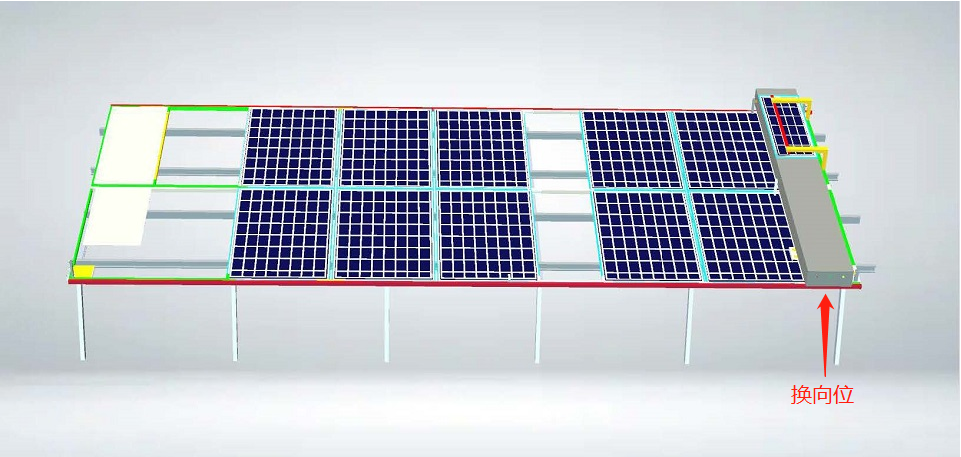
4. On the way back from the reversing position, it will eventually stop at the parking space
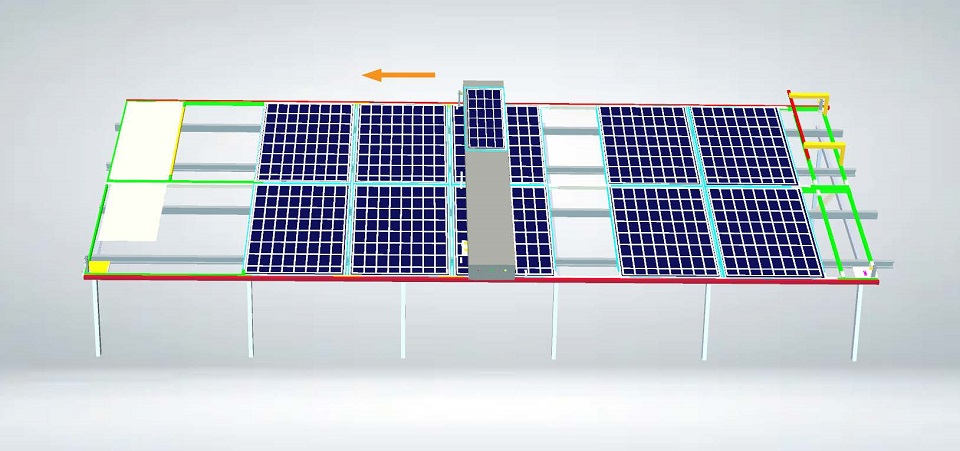
Battery charging
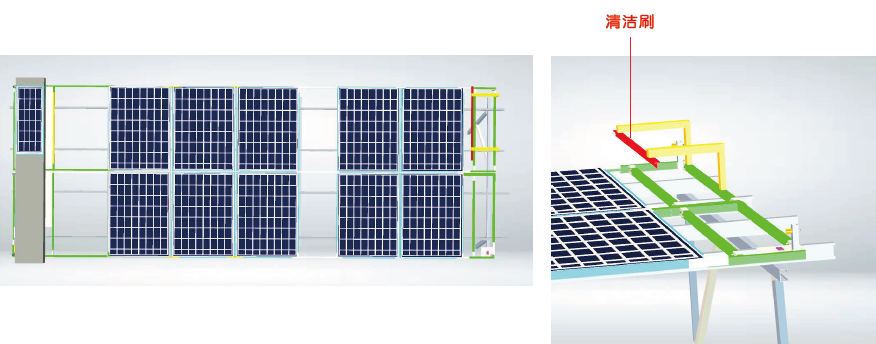
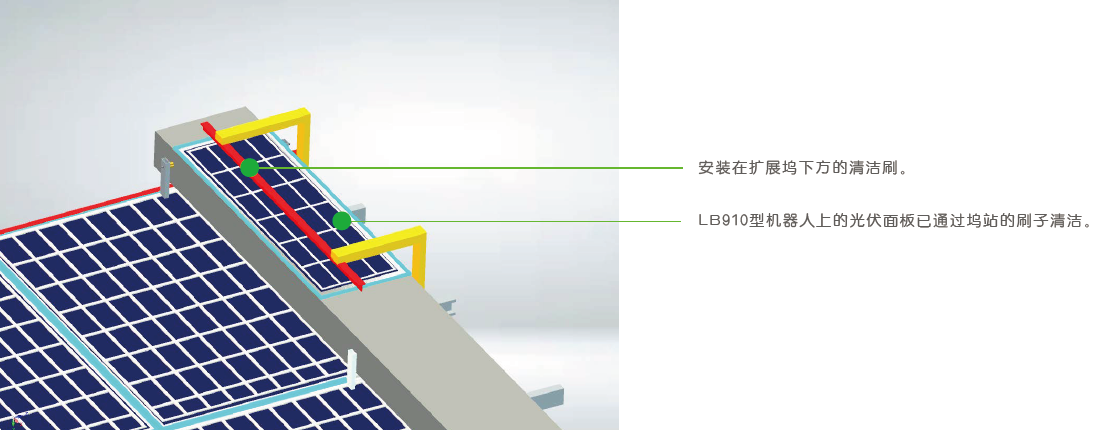
Robot system diagram
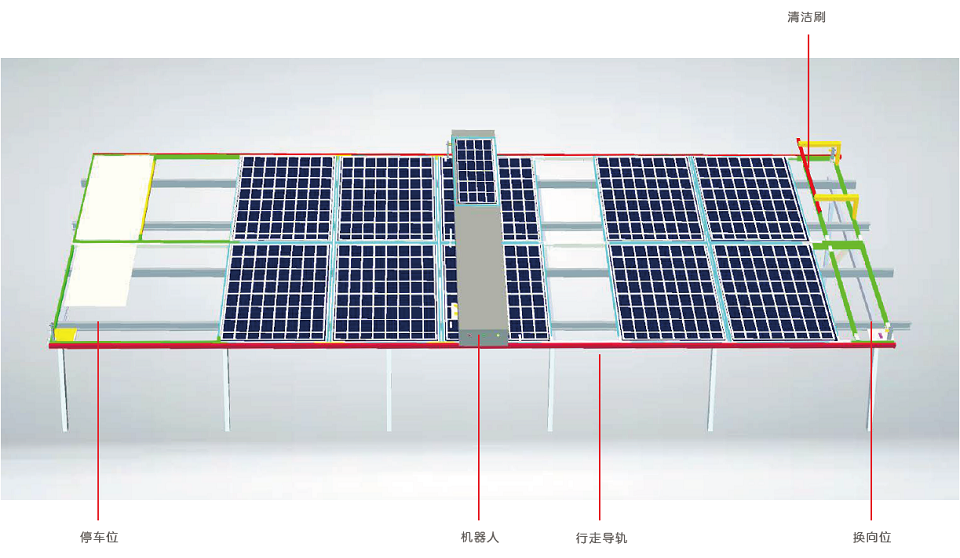
Installation process
1. Install parking spaces
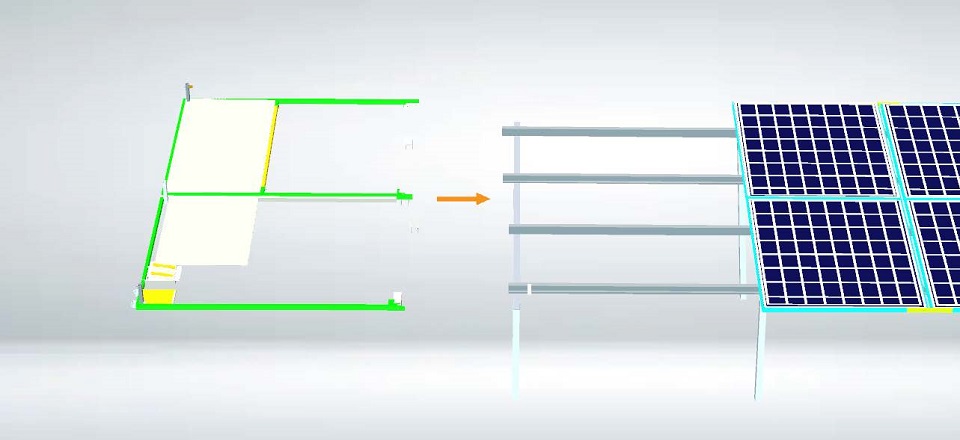
2. Install the reversing position
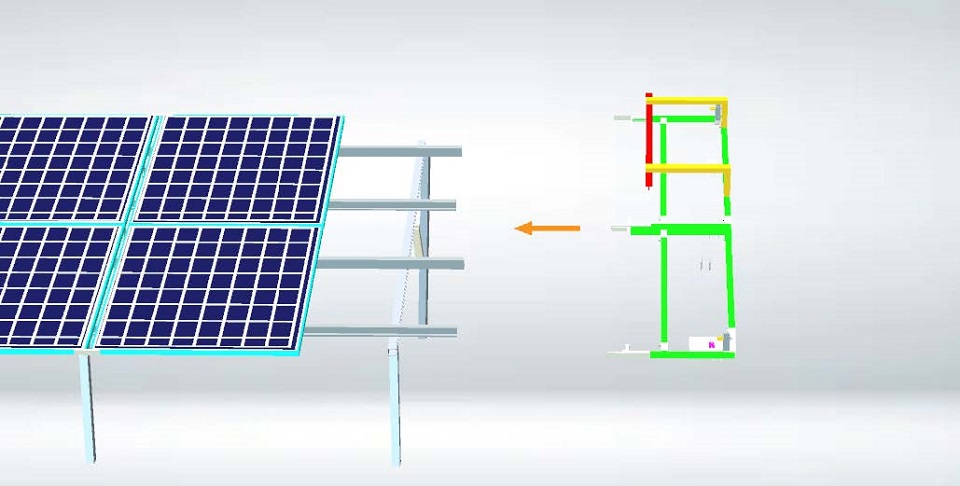
3. Install the upper and lower frame walking rails
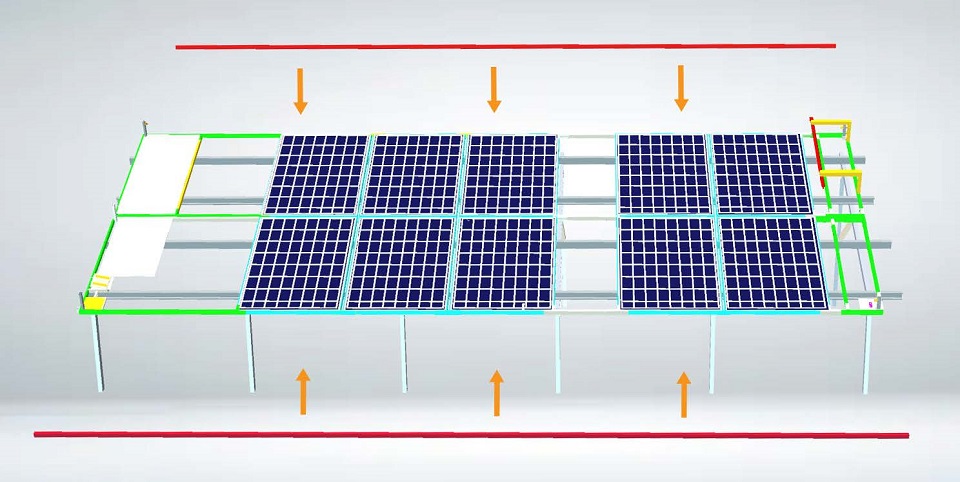
Small bridge between boards
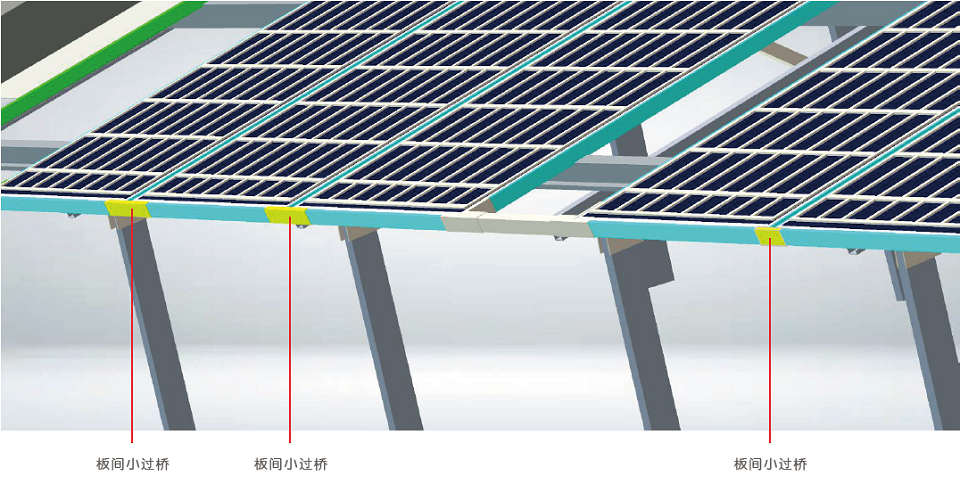
The small bridge between the boards is used for power stations that do not need to install walking rails, reducing robot vibration and saving costs.
Modular customization
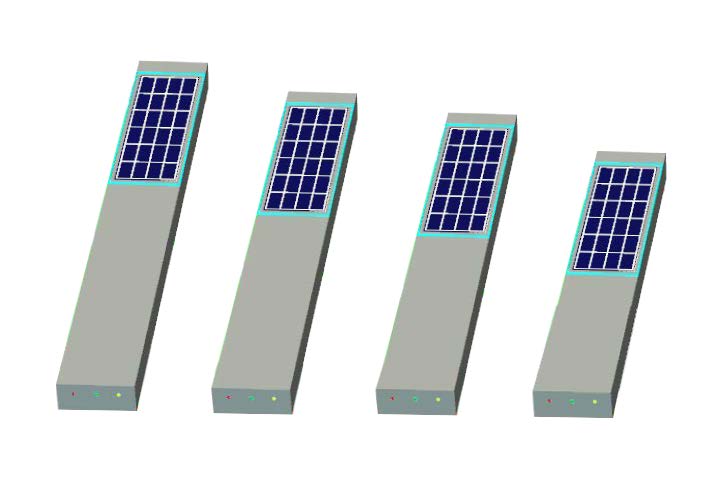
Battery solution
Single battery solution:
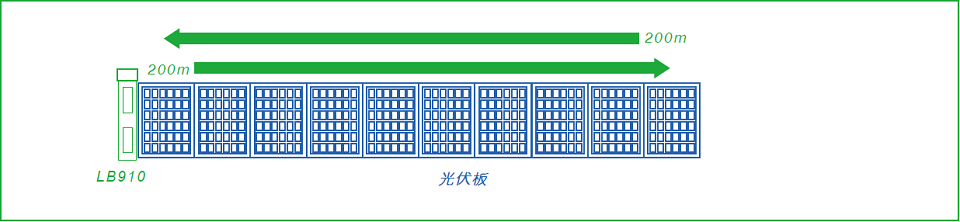
Dual battery solution:
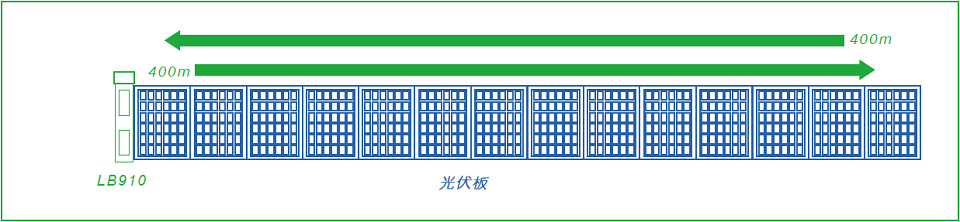
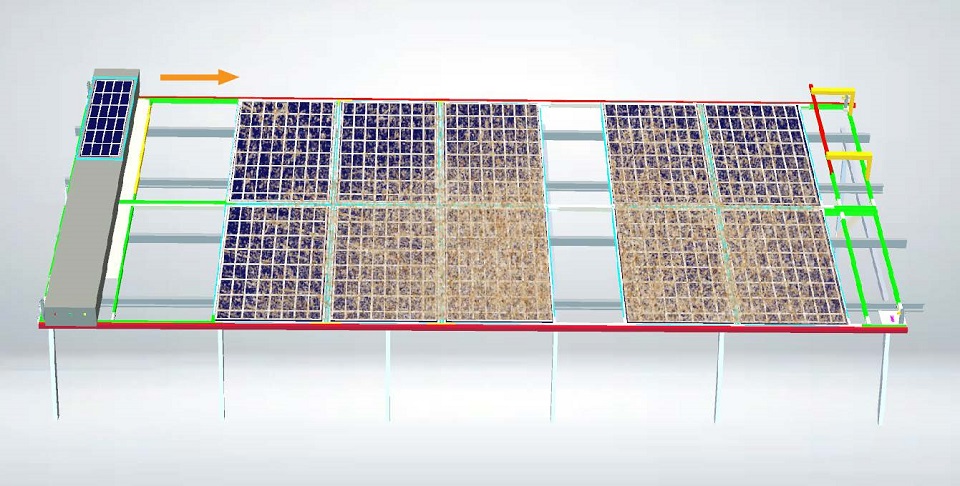
2. Cleaning in progress
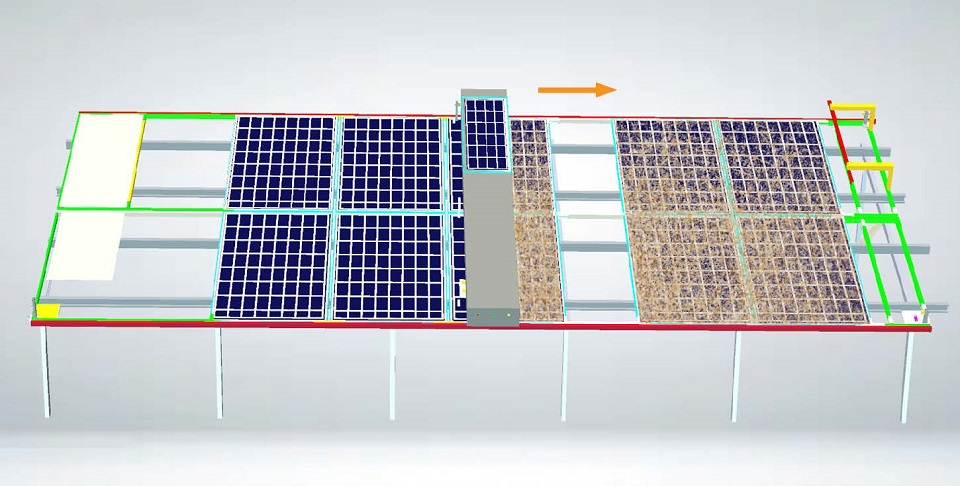
The LB910 robot moves along the upper and lower edges of the photovoltaic array, and the high-speed rotating roller brush can clean the dust on the surface of the module. In order to ensure the stable and smooth operation of the robot, and to protect the photovoltaic modules from crushing, it is necessary to install guide rails on the upper and lower ends of the photovoltaic panel array, and the robot moves along the guide rails. Sometimes, we just install small bridge rails between the components on the upper and lower sides of the photovoltaic panel array to reduce the vibration of the photovoltaic components when the robot is walking, and it can also protect the photovoltaic components.
3. The robot reaches the reversing position, ready to back
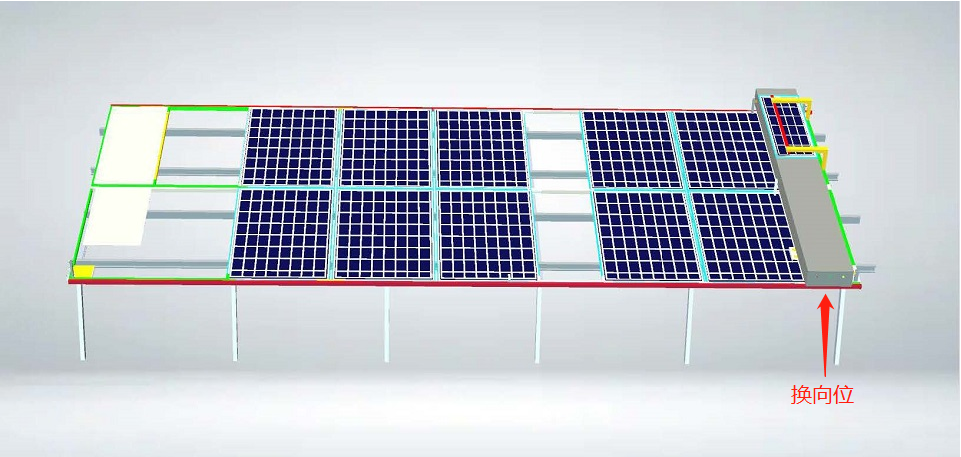
4. On the way back from the reversing position, it will eventually stop at the parking space
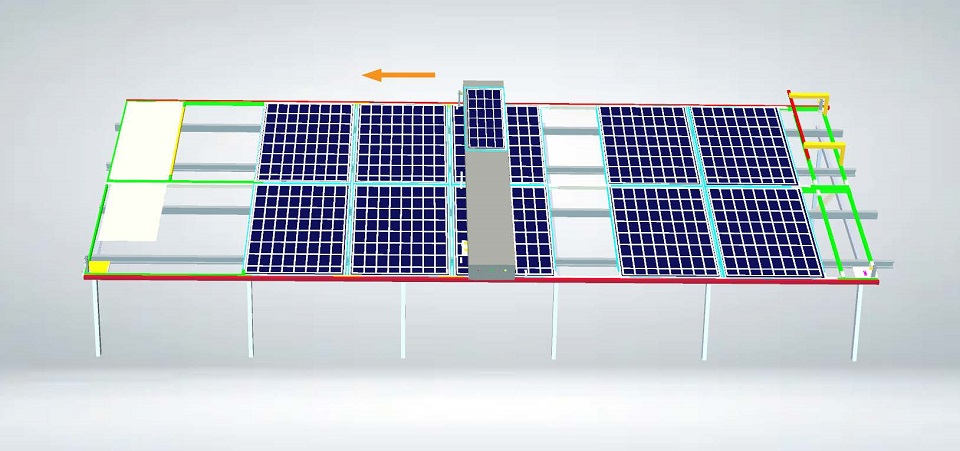
The robot can run fully automatically without manual cleaning.
After the robot completes a cleaning, it returns to the parking space. The function of the reversing position is to ensure that the robot can clean every photovoltaic panel, and sensors are installed on the reversing position to direct the robot to return in time after reaching the end.
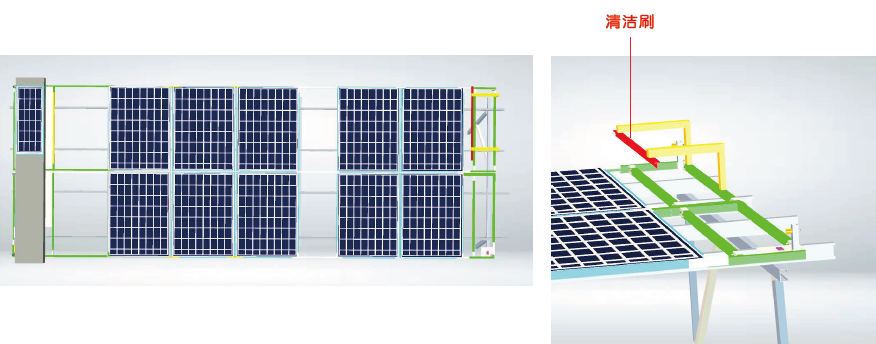
When the battery voltage is low, the LB910 robot can be charged through its own photovoltaic panel.
In order to ensure the high efficiency of charging photovoltaic panels, we install a fixed cleaning brush at the reversing position. When the robot moves to the reversing position, the fixed brush can clean the surface of its own photovoltaic panel.
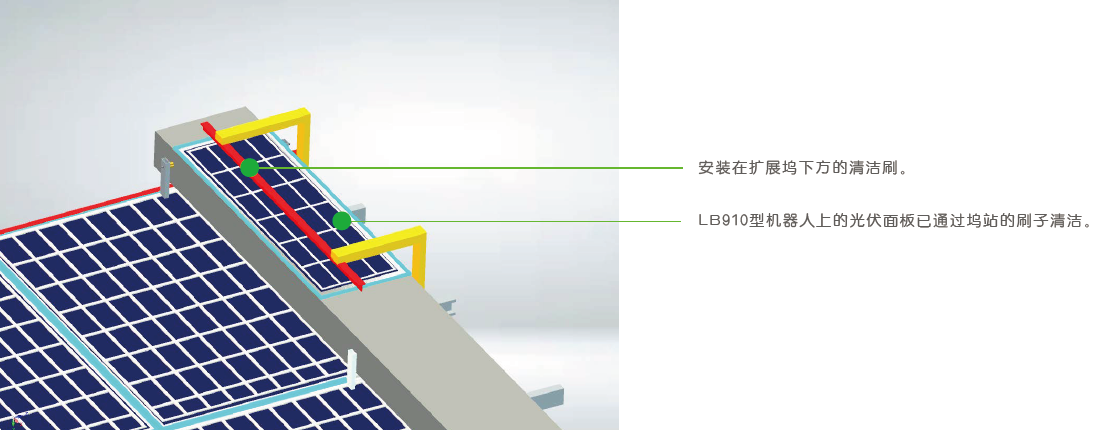
Robot system diagram
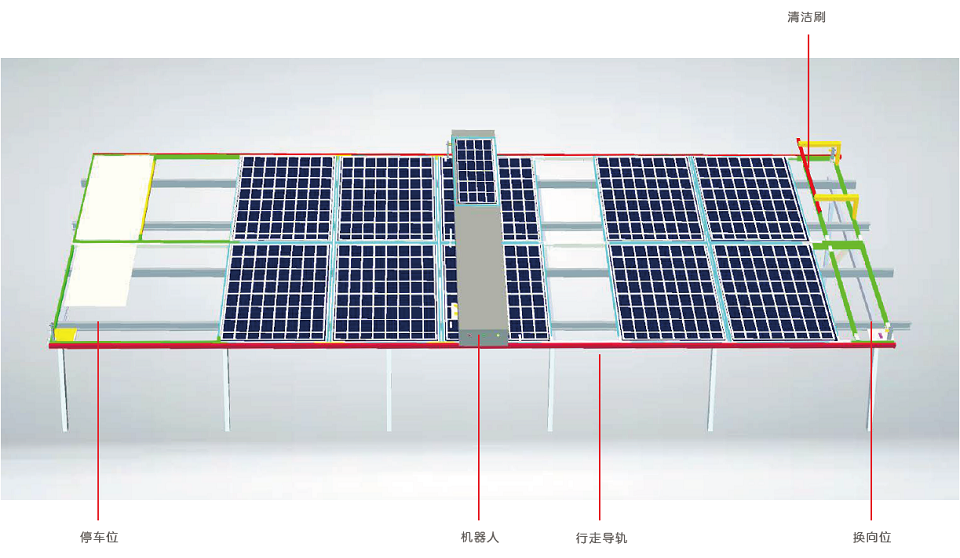
Installation process
1. Install parking spaces
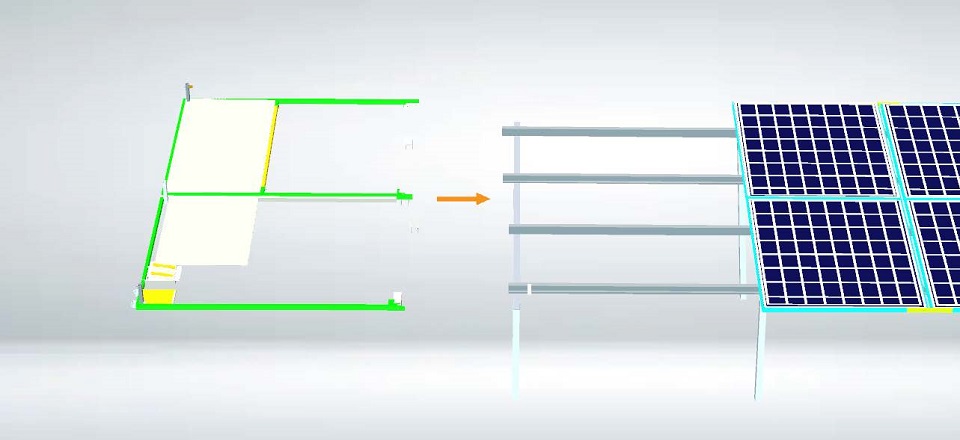
2. Install the reversing position
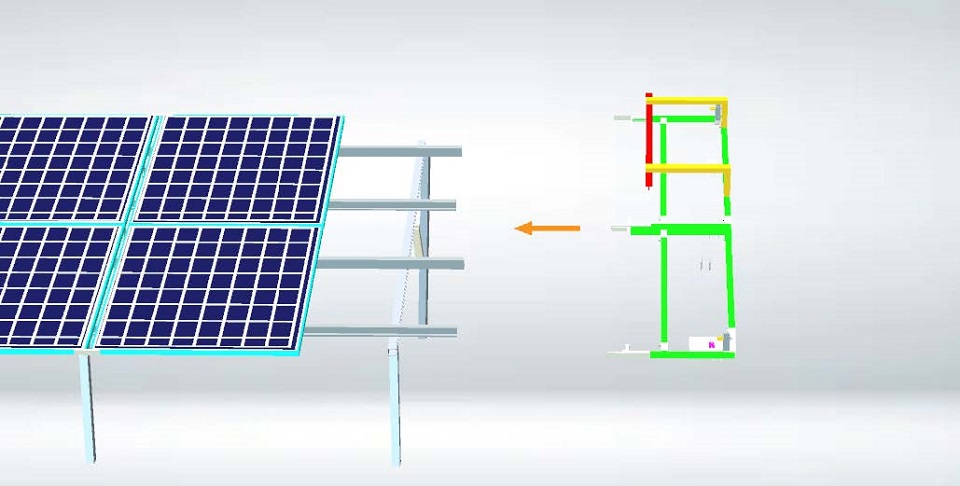
3. Install the upper and lower frame walking rails
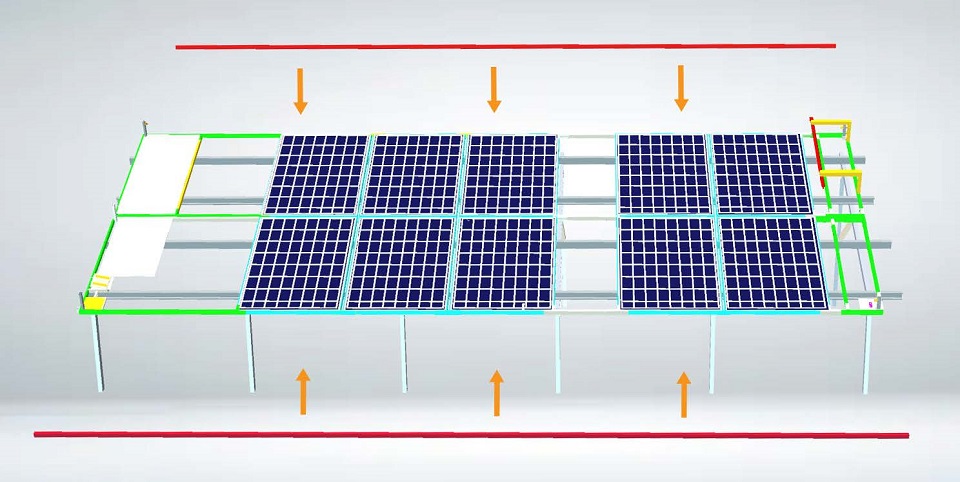
Small bridge between boards
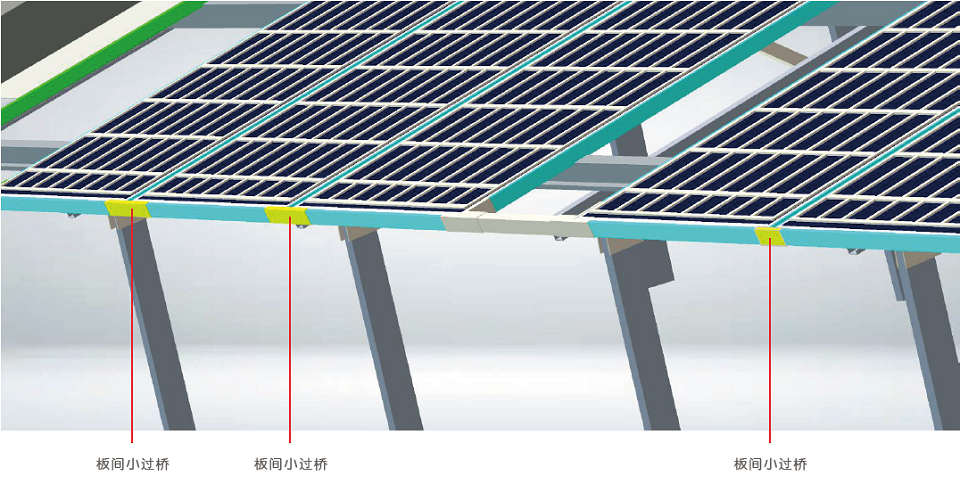
The small bridge between the boards is used for power stations that do not need to install walking rails, reducing robot vibration and saving costs.
Modular customization
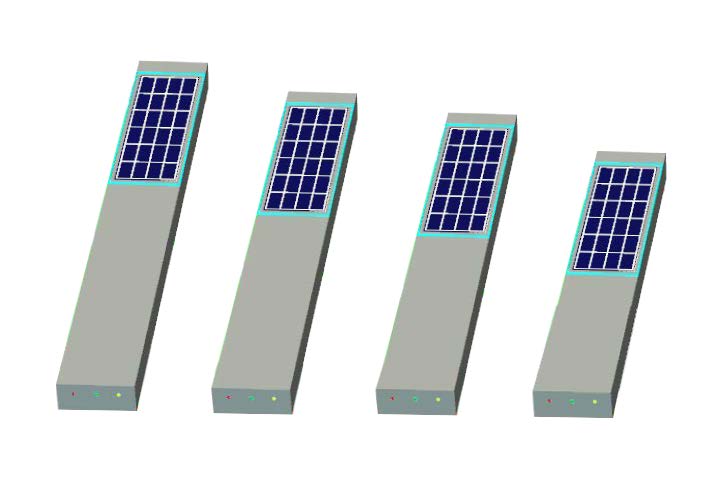
The LB910 robot can be customized according to the width of the photovoltaic panel array, and the length of the robot is from 2m to 6m to meet the needs of power stations with different widths.
Array bridge rail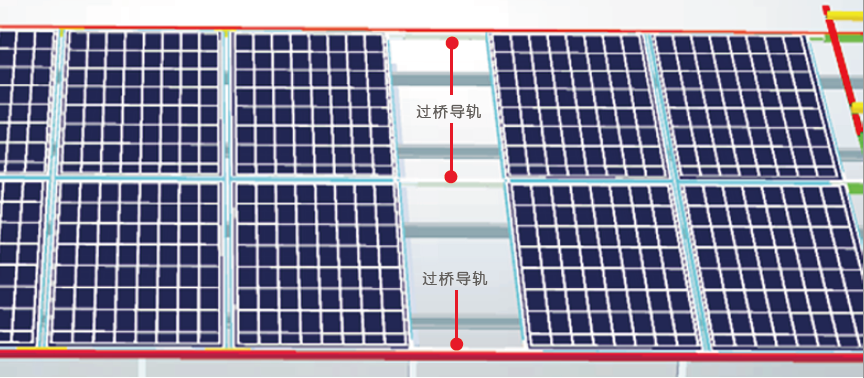
The bridge rails between the arrays need to be customized according to the site conditions, but the use of our company's modular components can speed up the on-site installation, and no welding tools are needed, which increases the flexibility and practicability of on-site installation.
*The length of the bridge rail should not exceed 3 meters.
*The gradient of the bridge guide rail does not exceed 30 degrees.
Feature
1. The robot runs fully automatically and starts at a set time every day or every few days without manual intervention. The cleaning process includes cleaning from left to right, and from right to left when returning. The robot has a manual operation mode, which can perform temporary cleaning at any point in time;
2. The robot can accept wireless remote control commands, and the management personnel can perform cluster control through the upper management software, including correcting the robot clock, modifying the startup time, commanding the robot to run in batches, and performing fault self-checking;
3. Compared with manual cleaning, the LB910 robot has a payback period of no more than 3 years. Regular cleaning can ensure that the photovoltaic panel is in the highest power generation state. In the event of a sandstorm or snowy weather, the power station management personnel can temporarily command the robot to travel through the upper software to achieve timely and rapid dust removal;
4. The design of the robot is sturdy and durable, can adapt to various complex working conditions, and the service life can reach 10 years. After working for a long time, some components need to be replaced, such as replacing the battery every 2-3 years and the brush every 3 years. Due to the modular design, it is convenient and time-saving to replace components on site;
5. The robot has strong weather resistance and is suitable for working in various extreme weather conditions. The working temperature is between -20℃ and 60℃. It can stay outdoors and work all year round;
6. The robot does not need external electricity, but is self-charged by its own photovoltaic panel. The battery can also be charged by 220VAC city power, or can be charged by the inverter of the photovoltaic power station;
7. It is powered by lithium battery and has a service life of more than 2 years. The battery capacity can guarantee the robot to work continuously for 2-3 hours;
8. Using antistatic nylon brush, the hardness of the brush will not scratch the surface of the photovoltaic module. The residue on the brush can be mechanically cleaned by a scraper;
9. The traveling speed of the robot is 12m/min, and the speed of the rotating brush is 300RPM;
10. The robot has an intelligent judgment function. When the power of the system drops too fast, the robot will turn back in time to prevent it from stopping in the middle of the array due to insufficient power.
The LB910 robot has single or double 24V/15Ah lithium batteries, depending on the length of the photovoltaic array.
The LB910 equipped with a single battery can clean the array of modules up to 200m in length (400m back and forth).
With the help of two batteries, the robot can complete the cleaning of photovoltaic arrays up to 400m in length (800 meters back and forth).
The battery power has sufficient safety margin to ensure that the robot will not stop on halfway due to insufficient power.
Single battery solution:
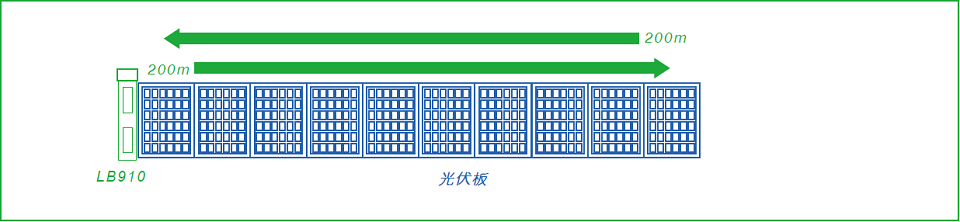
Dual battery solution:
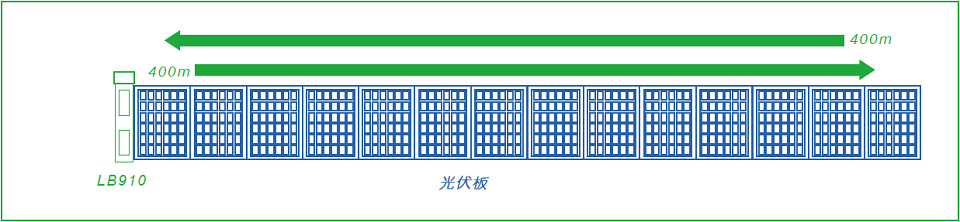
Technical Parameters
Marchine Technical Parameters | |
Applicable power station | Rooftop power station, fishing and light complementary power station, agricultural and light complementary power station, ground power station |
Driving medium | Edge rail or photovoltaic panel aluminum profile edge |
Weight | 30-60Kg |
Length | Customized according to the array width |
Operating temperature | -20~60℃ |
Brush type | Anti-static nylon brush, outer diameter 120mm |
PV panel safety | The brush does not scratch the surface of the component, and the robot does not crush the component |
Deceleration mechanism | Gearbox deceleration |
Running performance | |
Cleaning length | Up to 400 meters (800 meters back and forth) |
Sweeping width | 2-6m |
Climbing angle | <30° |
Travel speed | 12m/min |
Displacement of components up and down | <20mm |
Electrical parameters | |
Battery | 24V/15Ah |
Charge and discharge times | 2000 times |
Motor type | 24V DC brush motor |
Central control panel | MCU control |
Electrical performance standards | Compatible with electronic, safety and environmental standards |
Operating mode | Automatic/manual/wireless remote control, with functions of self-checking, fault feedback and parameter setting |
Wireless communication | ZIGBEE communication, support upper management software |
Waterless cleaning | Waterless design, dry brush with brush |
Automatic running | The robot starts running at a preset time |
Product model naming rules